वर नमूद केलेल्या कारणांव्यतिरिक्त, प्रक्रियेदरम्यान अॅल्युमिनियमचे भाग विकृत होतात. वास्तविक ऑपरेशनमध्ये, ऑपरेशन पद्धत देखील खूप महत्वाची आहे.
मोठ्या मशीनिंग भत्ते असलेल्या भागांसाठी, मशीनिंग प्रक्रियेदरम्यान उष्णता अपव्यय परिस्थिती चांगली आहे आणि उष्णता एकाग्रता टाळण्यासाठी, मशीनिंग दरम्यान सममितीय मशीनिंग वापरली पाहिजे. जर तेथे 90 मिमी जाड पत्रक असेल ज्यावर 60 मिमी पर्यंत प्रक्रिया करणे आवश्यक आहे, जर एका बाजूला मिल केलेले असेल आणि दुसरी बाजू त्वरित मिल केली गेली आणि अंतिम आकारावर एकदा प्रक्रिया केली गेली तर सपाटपणा 5 मिमी पर्यंत पोहोचेल; जर वारंवार फीड सममितीय प्रक्रिया वापरली गेली तर प्रत्येक बाजूने अंतिम आकारात 0.3 मिमीच्या सपाटपणाची हमी मिळू शकते. प्लेटच्या भागावर अनेक पोकळी असल्यास, प्रक्रियेदरम्यान पोकळी-दर-कॅव्हिटी अनुक्रमिक प्रक्रिया पद्धत वापरणे चांगले नाही, कारण यामुळे सहजपणे असमान शक्ती आणि भागांचे विकृतीकरण होईल. मल्टी-लेयर प्रोसेसिंग स्वीकारले जाते आणि प्रत्येक थर शक्य तितक्या एकाच वेळी सर्व पोकळींवर प्रक्रिया केली जाते आणि नंतर भाग समान रीतीने ताणतणाव करण्यासाठी आणि विकृती कमी करण्यासाठी पुढील थर प्रक्रिया केली जाते.
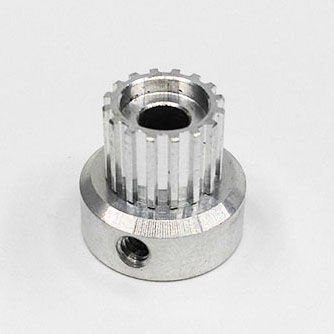
कटिंगची रक्कम बदलून कटिंग फोर्स आणि उष्णता कमी करा. कटिंग रकमेच्या तीन घटकांपैकी, बॅक-कटिंगच्या प्रमाणात कटिंग फोर्सवर मोठा प्रभाव आहे. जर मशीनिंग भत्ता खूप मोठा असेल तर पासची कटिंग फोर्स खूप मोठी आहे, जी केवळ भाग विकृत करणार नाही, परंतु मशीन टूल स्पिन्डलच्या कडकपणावर देखील परिणाम करेल आणि साधनाची टिकाऊपणा कमी करेल. जर आपण चाकूंची मात्रा कमी केली तर उत्पादन कार्यक्षमता मोठ्या प्रमाणात कमी होईल. तथापि, सीएनसी मशीनिंगमध्ये हाय-स्पीड मिलिंग वापरली जाते, जी या समस्येवर मात करू शकते. बॅक-बिगिंगचे प्रमाण कमी करताना, जोपर्यंत फीड अनुरुप वाढविला जातो आणि मशीन टूलची गती वाढविली जाते, प्रक्रिया कार्यक्षमता सुनिश्चित करताना कटिंग फोर्स कमी केली जाऊ शकते.
चाकूच्या ऑर्डरकडे देखील लक्ष द्या. रफ मशीनिंग मशीनिंग कार्यक्षमतेच्या सुधारणेवर आणि प्रति युनिट वेळ काढण्याच्या दराचा पाठपुरावा करण्यावर जोर देते. सामान्यत: अप-कट मिलिंग वापरला जाऊ शकतो. म्हणजेच, रिक्त पृष्ठभागावरील जास्तीत जास्त सामग्री वेगवान वेगाने आणि कमी वेळात काढली जाते आणि पूर्ण करण्यासाठी आवश्यक भूमितीय समोच्च मुळात तयार होते. समाप्त करण्याचा जोर उच्च सुस्पष्टता आणि उच्च गुणवत्तेचा आहे आणि डाऊन मिलिंग वापरला जावा. डाऊन मिलिंग दरम्यान कटर दातांची कटिंग जाडी हळूहळू जास्तीत जास्त ते शून्य पर्यंत कमी होत असल्याने, वर्क कडक होण्याची डिग्री मोठ्या प्रमाणात कमी होते आणि त्याच वेळी भागांच्या विकृतीची डिग्री कमी होते.
प्रक्रियेदरम्यान क्लॅम्पिंगमुळे पातळ-भिंतींवर वर्कपीस विकृत केले जातात आणि अगदी परिष्करण देखील अपरिहार्य आहे. वर्कपीसचे विकृती कमी करण्यासाठी, परिष्करण प्रक्रियेचा अंतिम आकार गाठण्यापूर्वी दाबणारा तुकडा सैल केला जाऊ शकतो, जेणेकरून वर्कपीस त्याच्या मूळ आकारात मुक्तपणे पुनर्संचयित होऊ शकेल आणि नंतर किंचित संकुचित होऊ शकेल, कठोर क्लॅम्पिंगच्या अधीन वर्कपीस (संपूर्णपणे हाताने), आदर्श प्रक्रिया प्रभाव अशा प्रकारे मिळू शकतो. थोडक्यात, क्लॅम्पिंग फोर्सचा कृतीचा बिंदू आधारभूत पृष्ठभागावर सर्वोत्तम आहे आणि क्लॅम्पिंग फोर्सने वर्कपीसच्या चांगल्या कडकपणाच्या दिशेने कार्य केले पाहिजे. वर्कपीस सैल होणार नाही याची खात्री करण्याच्या आधारे, क्लॅम्पिंग फोर्स जितके लहान असेल तितके चांगले.
पोकळी असलेले भाग मशीनिंग करताना, मिलिंग कटरला ड्रिल बिट सारख्या भागामध्ये थेट डुंबू न देण्याचा प्रयत्न करा, परिणामी मिलिंग कटर, अनसमथ चिप काढून टाकणे आणि जास्त तापविणे, विस्तार आणि साधन कोसळण्यासाठी अपुरी चिप जागा. तुटलेल्या चाकूसारख्या प्रतिकूल घटना. प्रथम, मिलिंग कटर किंवा एक आकाराच्या आकाराच्या समान आकाराच्या ड्रिलसह छिद्र ड्रिल करा आणि नंतर मिलिंग कटरने गिरणी करा. वैकल्पिकरित्या, सीएएम सॉफ्टवेअरचा वापर सर्पिल कटिंग प्रोग्राम तयार करण्यासाठी केला जाऊ शकतो.